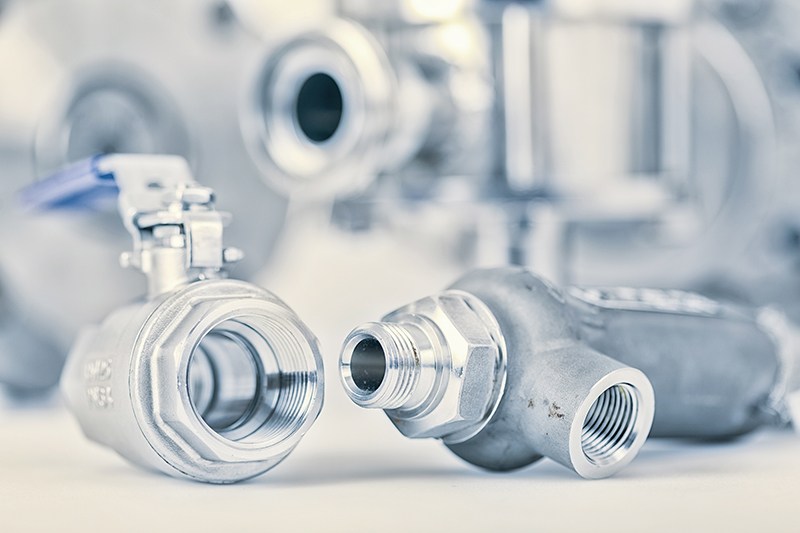
Pumps and pipelines are commonly recognised in Australia as requiring additional consideration in fluid transportation system design. Pump and pipe design significantly impacts fluid and pressure properties throughout the system, as most would agree. However, the location of the valves in Australia is equally as crucial as the kind of valves utilised in the system. Correctly positioned valves may extend the life of a system, save maintenance costs, eliminate cavitation effects, and improve system efficiency. The Australian market for industrial valves was worth $580 million in 2017 and is predicted to reach $1.3 billion by 2023. Additionally, we’ll go through valve selection and location and provide general practice advice.
A Valve’s Importance.
There are precise rules and regulations for each factor in designing a pipe system. Still, valves are typically purchased and installed according to those guidelines regardless of the operating pressure, temperature, or fluid type handled inside the system. As a result, the following criteria must constantly be considered while choosing valves and placing them within the system:
General Valve Wear.
The degree of degradation (or “wear”) that a valve must withstand throughout its lifespan is essential in valve selection. When it comes to deterioration of valves, a variety of factors need to be taken into account, including corrosion (how corrosive is the fluid flowing through the valve? Because fluids like acid and water do not have the same chemical properties, this requires to be taken into account), scrape (the roughness of the liquid flowing through the valve? (with significant temperature divergences during the function of a valve, one can face difficulties with growth and compaction factors).
Cavitation.
Pumps may suffer catastrophic failure due to the well-known phenomena of cavitation. Cavitation, on the other hand, is a significant issue with valves. In a valve, cavitation causes localised impact damage to the body and internals by generating intense shock waves. The efficiency and longevity of one’s system’s valves may be improved by reducing cavitation. Cavitation will be discussed in further detail in Section 4 of this article.
A flashing.
Cavitation and flashing are two terms that describe the same phenomenon. In contrast to cavitation, the damage caused by flashing is far more widespread and affects a much smaller area of your system. When flashing occurs, one’s system is filled with liquid and vapour. Physical collision and chemical interaction between moisture and pipe material might result in significant damage. Corrosion and erosion may be reduced by reducing the likelihood of flashing in the system. For the most part, this article will cover cavitation since flashing and cavitation arise from the same principles and maybe decrease utilising the same suggestions given.
Conclusion.
As a final point, this article has discussed the many aspects of fluid mechanics and how they affect the efficiency of a fluid transportation system. This article should be applied to a fluid transportation system that is currently under development or has already been built to discover how the previously described elements might affect the valves within the system. With practice, one may know how valves in Australia are made to work in various situations. As a result, one may be certain that the valve will function adequately and not impede the system’s overall performance by choosing and positioning the ideal valve for the task at hand.